Space & SATELLITE
Proven Solutions for Demanding Space and Satellite Applications
Trusted by
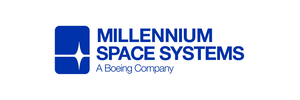
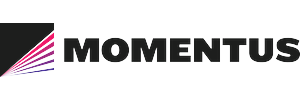
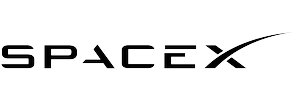
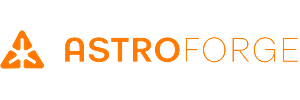
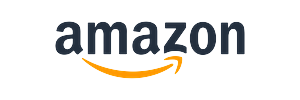
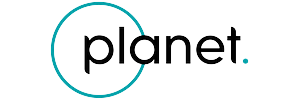
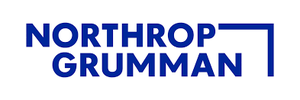
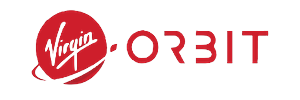

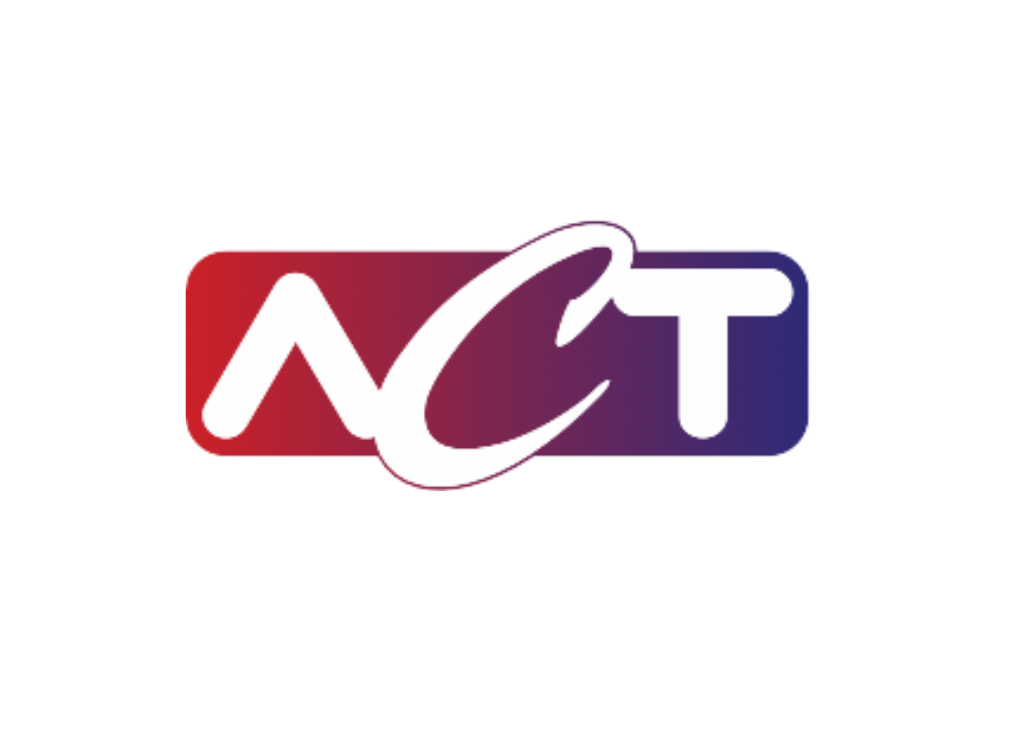
Payload Panels and Composite Tubes
ACP’s composites solutions are engineered with precision to support the evolving needs of satellite manufacturers, space agencies, and aerospace companies globally. With years of expertise in the space sector, our team works tirelessly to ensure every product we create exceeds industry standards for reliability, performance, and cost-effectiveness.
Composite Bus & Payload Structures
Our sandwich panels combine lightweight composites with high-strength core materials, offering exceptional durability and thermal performance for payload panels and satellite structures.
Solar Array Substrates
Lightweight composites are used in the construction of solar arrays, solar wings, deployable booms, and more.
Composite Tubes
Our Composite Tubes serve as lightweight and durable frameworks for solar arrays and payloads, offering significant weight savings compared to traditional materials.
Composite Structures
We offer flat carbon structures with high-temperature curing capabilities, making them ideal for thermal applications in satellites.
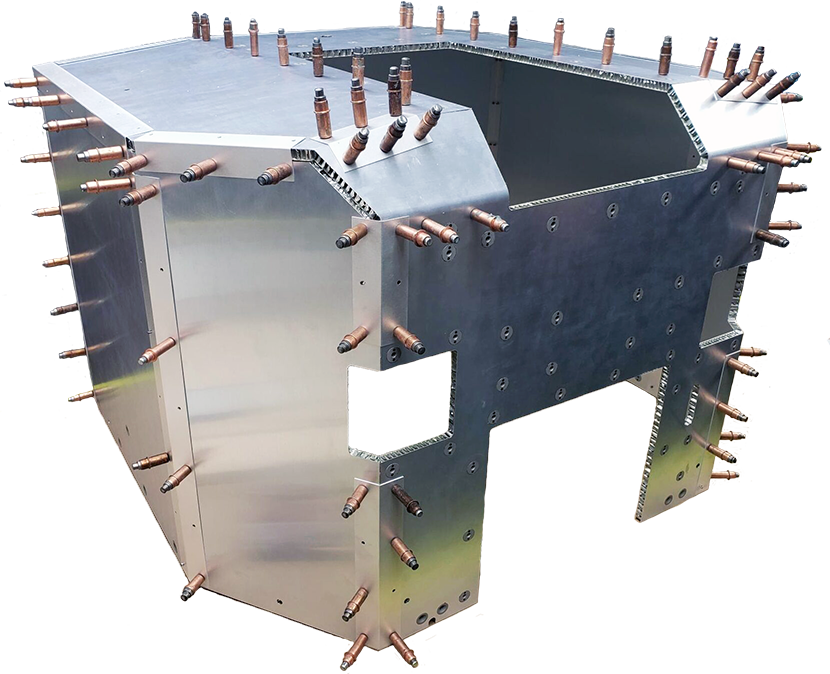
Structural Core
- Carbon Honeycomb
- Aluminum Honeycomb
- Aramid Honeycomb
Materials-Facesheets
- Aluminum - All Grades
- Carbon Fiber
- Hybrid Facings
Fixtures & Inserts
- Aluminum
- Titanium
- INVAR
- CFRP
Need to discuss your materials requirements?
Light on Weight, Heavy on Innovation.
Our sandwich panels and aerospace components are engineered with space missions in mind. Whether you’re designing a small communication satellite or a large Earth observation satellite, our team works closely with you to ensure the materials meet your project’s unique needs. We provide comprehensive manufacturing support, from initial design to final delivery.
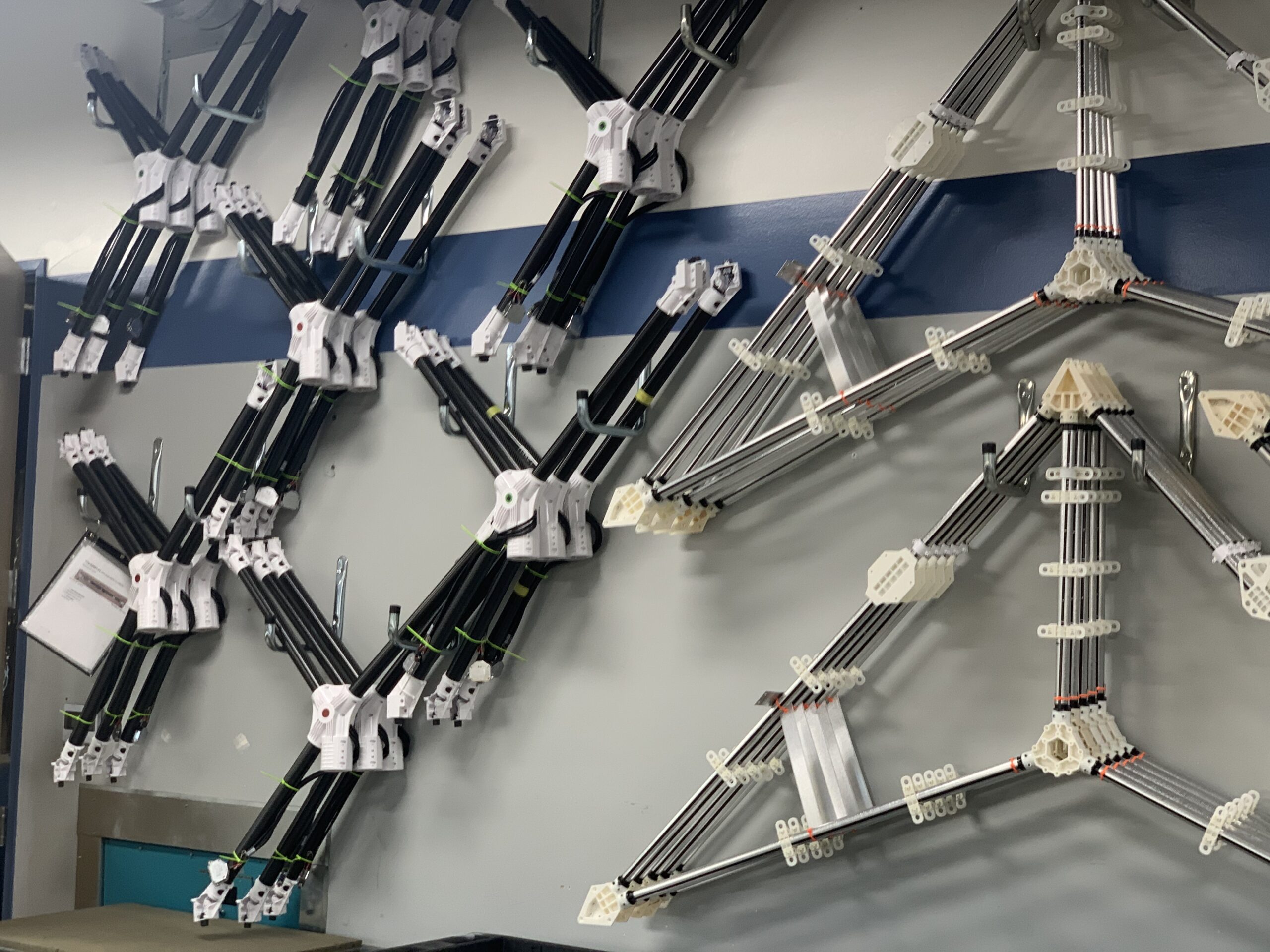
STRUCTURAL SUPPORT COMPONENTS
We provide custom-engineered structural components that offer optimal strength-to-weight ratios for various satellite designs.
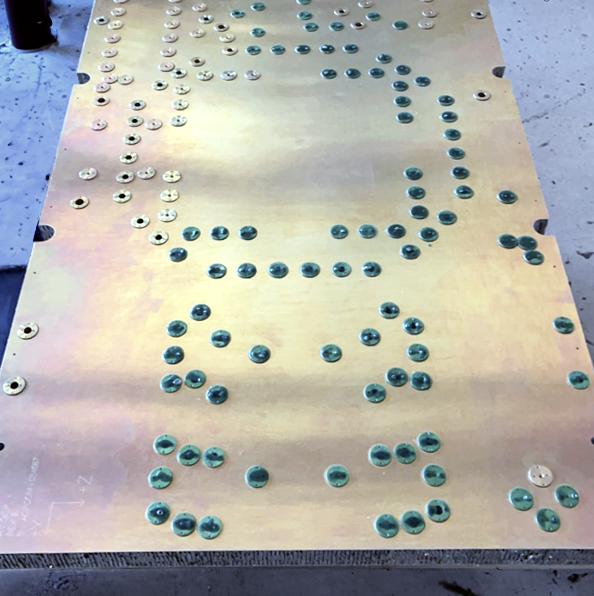
Assembly, Inserts and Fixturing
We provide assembly, fixtures and inserts that meet the strict requirements of space applications while ensuring reliable performance in extreme environments.
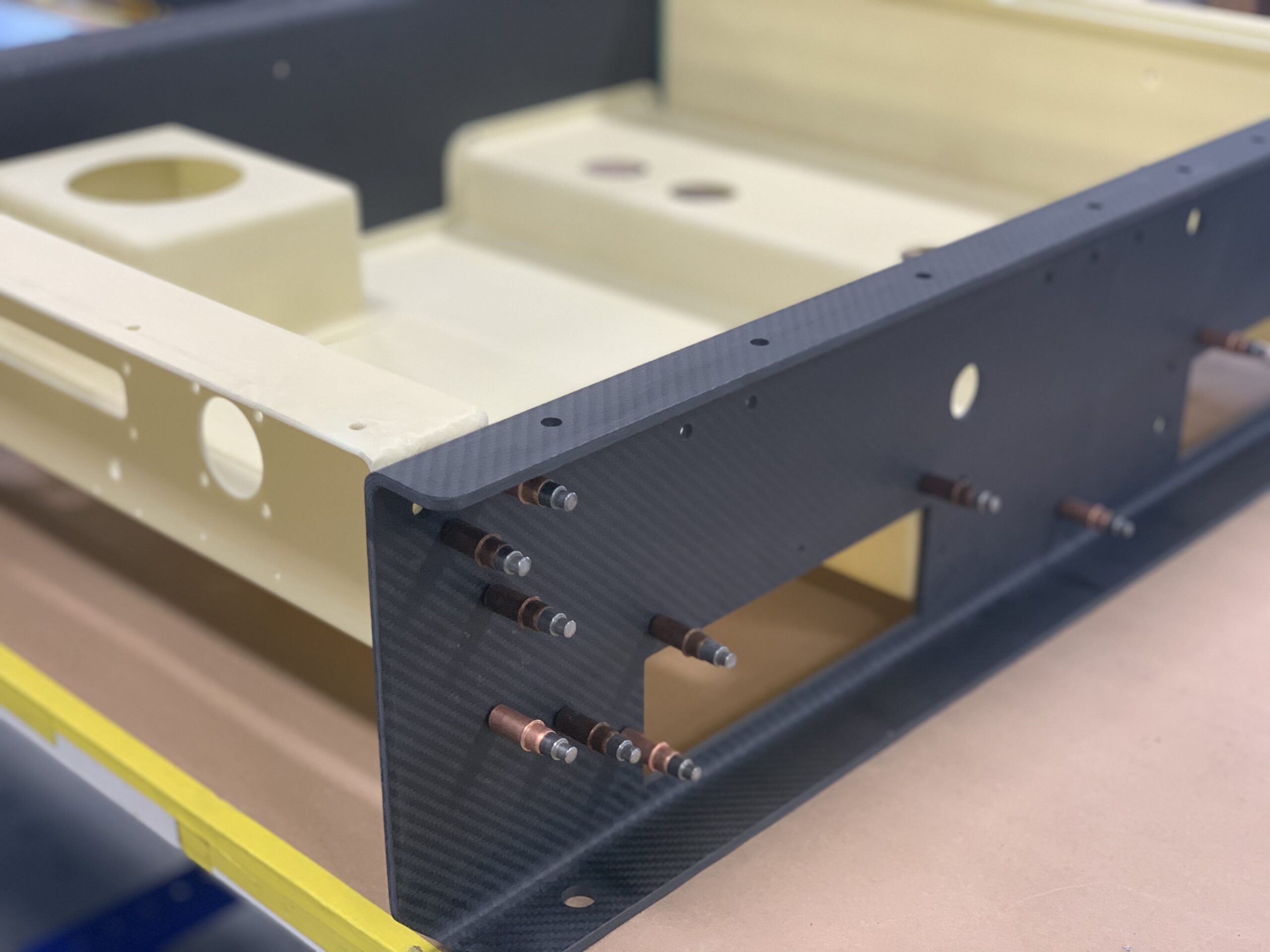
Thermal Protection Components
Our thermal protection systems are designed to withstand extreme temperature fluctuations, ensuring satellite components remain safe and functional during launch and orbit.
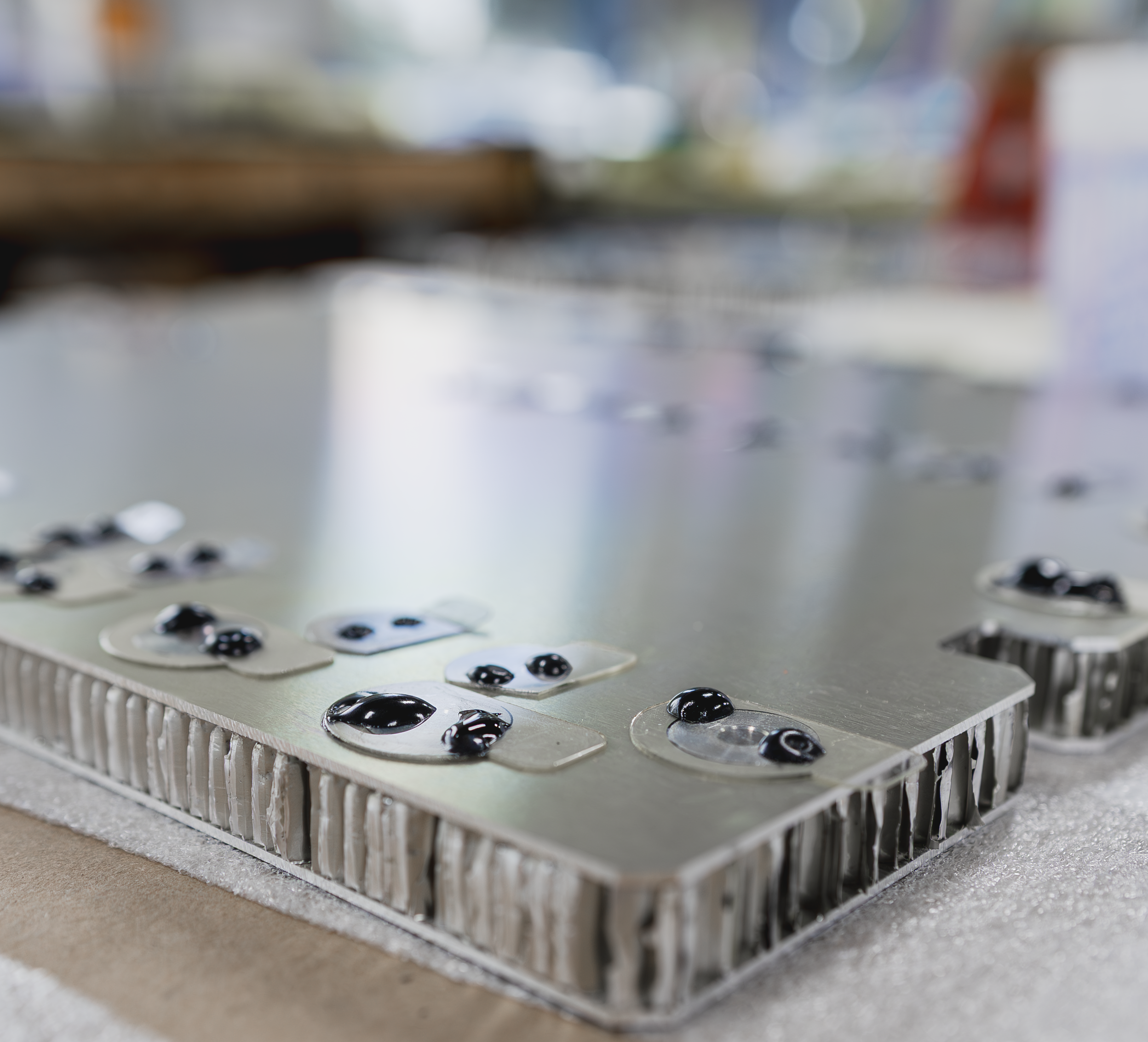
Custom Engineering Solutions
Not all space missions are the same. We offer tailored solutions to meet the unique needs of your satellite project, ensuring performance, efficiency, and reliability.
From Concept to Orbit: Lightweight, Reliable, Efficient.
ACP Composites has extensive expertise in satellite composite manufacturing, demonstrated through our involvement in numerous notable projects. We have a proven track record of delivering reliable and high-performance solutions for:
- Communication Satellites
- Earth Observation Satellites
- Scientific Research Satellites
- Military Satellites
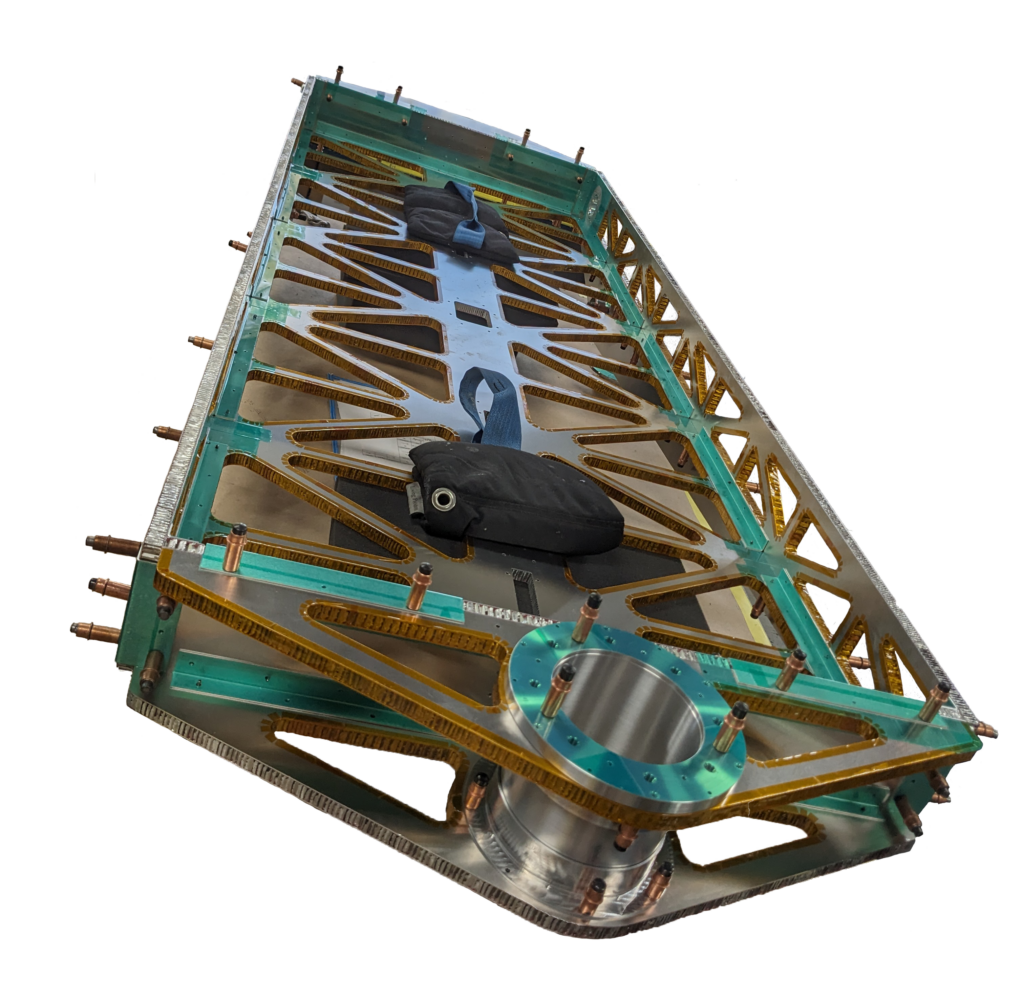
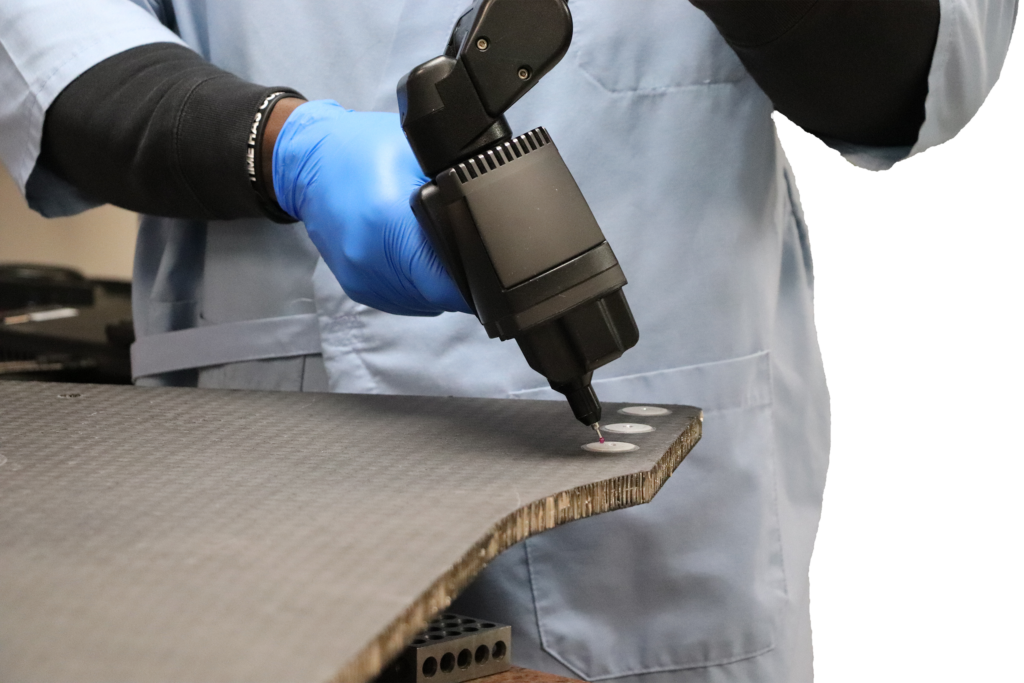
Quality is our Design
At ACP Composites, our commitment to quality and innovation is at the core of everything we do. Through a combination of advanced manufacturing processes, specialized materials, state-of-the-art inspection equipment, and rigorous quality assurance practices, we ensure each component conforms to your specific quality requirements so your space systems can operate reliably in the unforgiving conditions of space.
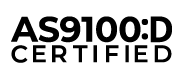
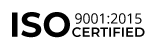
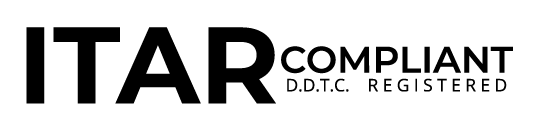
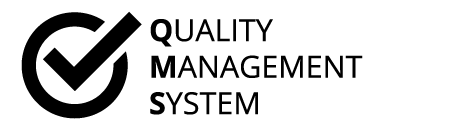
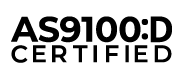
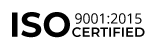
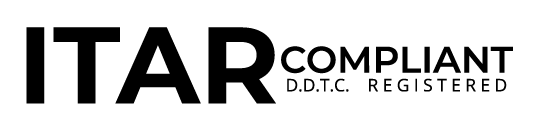
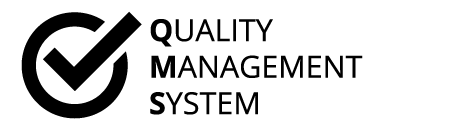
SMARTER DESIGN. LIGHTER SATELLITES.
With ACP Composites Satellite Bus Panels
Our satellite bus panels are integral to the structural framework of your satellite. These panels provide the foundation for all satellite systems, housing critical components such as propulsion, communication systems, and thermal control. With a focus on structural integrity, weight reduction, and ease of integration, our bus panels are engineered to meet the demanding conditions of space.
Our composite bus panels offer superior mechanical strength while minimizing weight, ensuring the satellite remains stable and resilient during launch and throughout its mission. Additionally, our panels are customizable to fit the unique design and integration requirements of your satellite’s bus system.
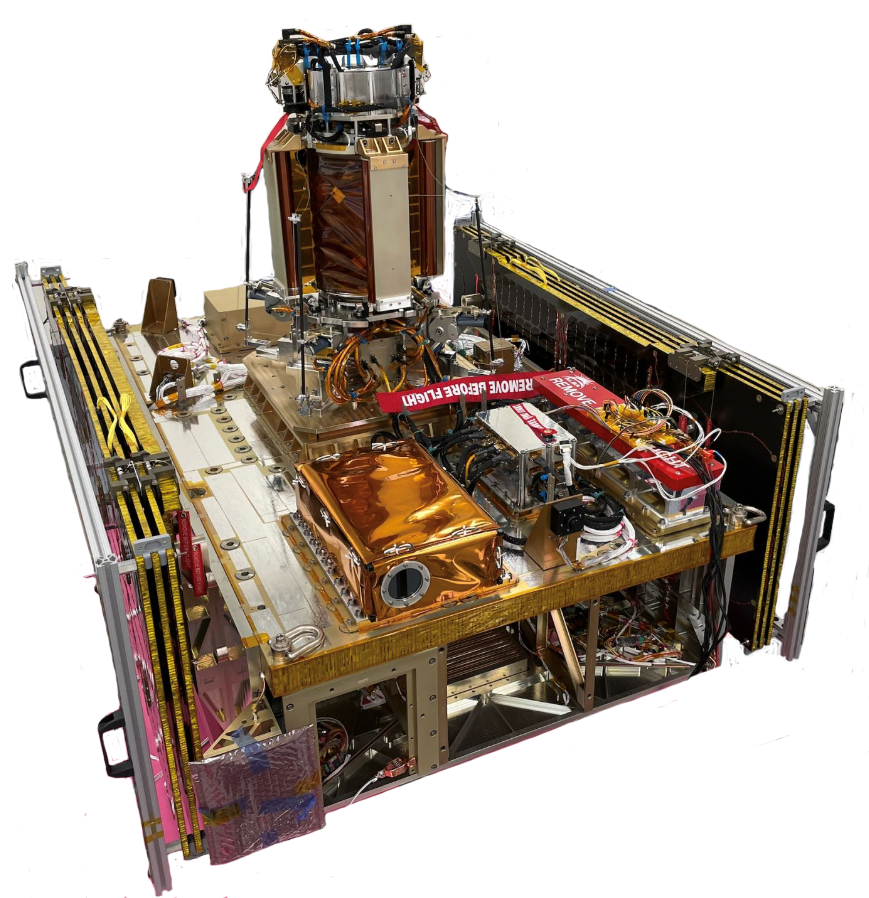
unleashing the Potential of composites
We understand that space exploration is not just about pushing the limits of technology—it’s about making that technology reliable, efficient, and sustainable. Our mission is to help space missions succeed by providing lightweight, durable, and customizable materials that improve satellite performance and reduce launch costs.
Lightweight
Reduces overall satellite weight, contributing to more cost-effective launches.
High Strength
Ensures structural integrity even in extreme conditions.
Thermal Performance
Maintain thermal stability, ensuring the satellite’s components remain within operational temperatures.
Seamless Integration
Designed for easy integration into satellite bus architectures, compatible with a wide range of satellite designs.
Custom Solutions
Tailored to meet the unique needs of your satellite’s structural and design requirements.
Frequently Asked
Questions
Can’t find what you’re looking for?
Please reach out to our experts.
Satellite composite parts are components made from advanced composite materials, such as carbon fiber, fiberglass, and Kevlar, which are used to construct various parts of a satellite. These parts include structural elements, panels, bus panels, solar arrays, and more. Composites are preferred due to their lightweight, strength, and durability, which are crucial for satellite performance in space.
Composites are used in satellites because they offer several key benefits:
- Lightweight: Reduces the overall mass of the satellite, which lowers launch costs.
- High Strength-to-Weight Ratio: Provides strength and rigidity while maintaining a light weight.
- Durability: Resistant to extreme temperatures, radiation, and mechanical stresses encountered in space.
- Thermal Stability: Excellent at managing heat, which is essential for satellite operations in space.
Composites are used in several key satellite components:
- Satellite Bus Panels: These panels provide structural support for the satellite, housing critical systems like propulsion and communications.
- Solar Arrays: Lightweight composites are used in the construction of solar arrays, enabling efficient power generation.
- Thermal Insulation and Heat Shields: Composites are ideal for managing temperature extremes in space.
- Structural Frames and Panels: Composites form the framework for satellite payloads, ensuring rigidity while minimizing weight.
The benefits include:
- Reduced Launch Costs: Lighter satellites are more cost-effective to launch.
- Increased Payload Capacity: Less weight means more room for essential payloads.
- Enhanced Efficiency: Lightweight materials help optimize fuel consumption and power efficiency.
- Improved Performance: Composites provide better structural integrity, thermal stability, and resistance to space conditions.
Yes, composite materials are engineered to withstand the extreme conditions of space, including high levels of radiation, temperature fluctuations ranging from -250°F to +250°F, and mechanical stresses during launch and deployment. Composites like carbon fiber and fiberglass are used for their ability to maintain structural integrity under these conditions.
Composites are essential in thermal management systems for satellites. They can be designed to provide passive thermal control, such as using sandwich panels that insulate against heat or distribute thermal energy effectively. Composite materials also have low thermal expansion rates, helping to maintain the satellite’s structural stability despite the extreme temperature shifts in space.
Composite parts in satellites are designed for long-term durability, with lifespans often exceeding 10-15 years, depending on the specific satellite mission. The materials are resistant to the degradation caused by radiation, temperature extremes, and other environmental factors in space, which helps ensure that the satellite performs optimally throughout its mission.
Yes, composite satellite parts are highly customizable. We can tailor the design, material, and dimensions to meet the specific needs of a satellite mission, including the type of orbit, payload requirements, and environmental conditions. Custom solutions are often required for specialized applications like Earth observation, communication satellites, or space exploration.
Composite satellite parts are manufactured using advanced techniques like lay-up molding, autoclave curing, and composite panel press cure. These methods allow for the creation of highly precise and robust components. The materials are layered and cured under controlled conditions to achieve the desired strength, weight, and thermal properties for space applications.
Composite satellite parts generally require little to no maintenance during their operational life in space, as they are designed to be durable and resilient to harsh space conditions. However, the satellite’s ground support systems may require monitoring, and some components may need to be inspected for wear or damage during regular satellite health checks or at specific mission milestones.
Yes, despite the initial higher material cost, composite parts are highly cost-effective in the long run. The reduction in weight leads to lower launch costs, and the long-lasting durability of composites ensures that satellite systems can remain operational for extended periods without frequent replacements or repairs.
Composite materials are often preferred over traditional materials like aluminum for certain satellite components due to their superior strength-to-weight ratio, thermal stability, and resistance to radiation. While aluminum is still used in some satellite structures, composites offer more advanced performance in many areas, particularly for reducing weight and enhancing durability.
Yes, composite materials are often chosen for satellite components exposed to high radiation because they are more resistant to radiation damage compared to traditional metals. Specialized composites can be designed to maintain their structural integrity and performance under high-radiation environments, ensuring the satellite continues to function in space.
Sandwich panels combine a lightweight core material with high-strength outer layers, providing excellent thermal insulation, structural integrity, and impact resistance. These panels are ideal for use in satellite structures, where they help reduce weight while offering the necessary strength to support payloads and other critical components.